Odoo Manufacturing Order (Odoo Manufacturing Module)
Identifying the raw materials to produce the product, setting up a workstation for processing the raw materials, tracing the product movement, managing by product variants, and so on are all part of the manufacturing order.
Improper management of these elements causes manufacturing delays, which may result in the order being canceled, resulting in financial and productivity losses for the organization. Odoo manufacturing order
Let's look at how to create a Manufacturing Order with Odoo Manufacturing Module.
Consider the following example for a wooden table manufacturing process. To begin, the components or raw materials required for manufacture are given, such as the tabletop, table legs, and a few screws and bolts. Second, cutting, carving, assembling, finishing, hand painting, and packing are all essential tasks.
Finally, work centers will be established and allocated to carry out production tasks.
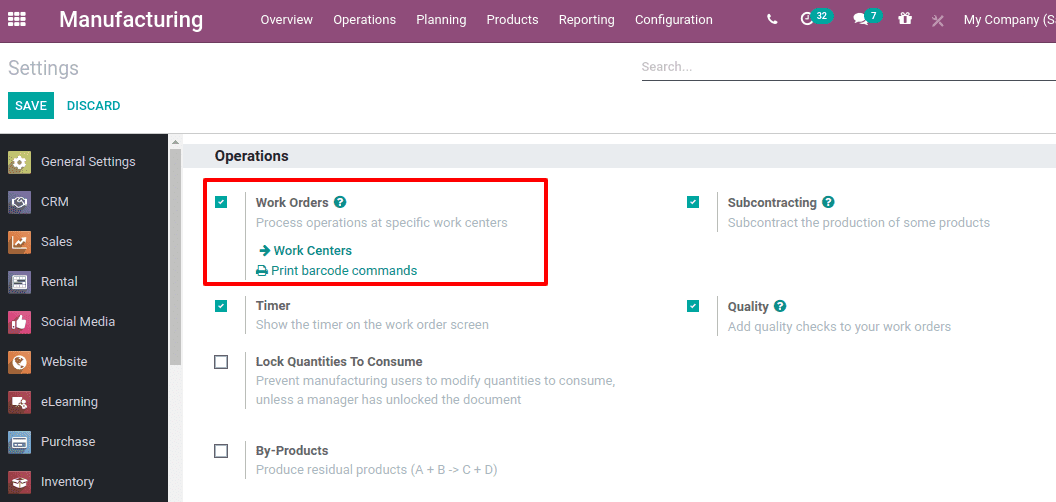
Odoo Manufacturing Order
A manufacturing order is created in three steps with Odoo Manufacturing Module.
Step 1: Establish a work center
Odoo Manufacturing Module > Configuration > Work centers can be used to construct a work center. The ‘work order' must be enabled from the manufacturing configuration settings to make the work center visible in the configuration menu.
Then establish and configure a production work center.
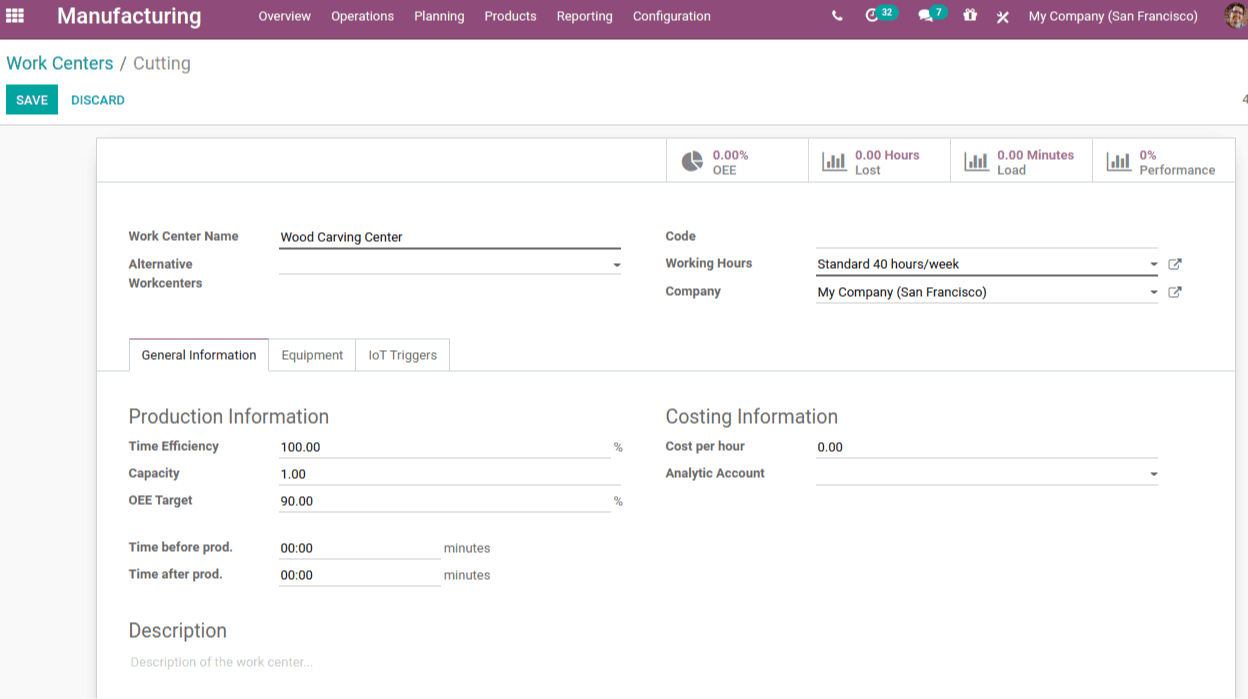
Name of Work Center: This is the name of the work center.
Alternative Work Centers: If the primary work center is occupied with another operation, employ a substitute work center.
Code: This is the code for the work center.
Working Hours: Work hours are set by the company.
In the case of a multi-company work center, the company to which this work center belongs.
Under the heading "General Information,"
Calculates the expected duration of a work order at this work center using time efficiency. The predicted duration will be one hour if the work order takes one hour and the efficiency factor is 100 percent. The predicted time is 30 minutes if the efficiency factor is 200 percent.
Capacity: The number of items that can be produced simultaneously.
OEE (Overall Equipment Efficiency) Target: A percentage-based target for overall equipment efficiency.
Prior to Production: Time to set up in minutes
Time after production: Cleaning time in minutes
Cost per hour: The hourly cost of running a work center.
Add an analytical account to your production orders if you want automatic analytic accounting entries.
Add the equipment utilized in the work center, as well as the technician who owns it, to the Equipment tab.
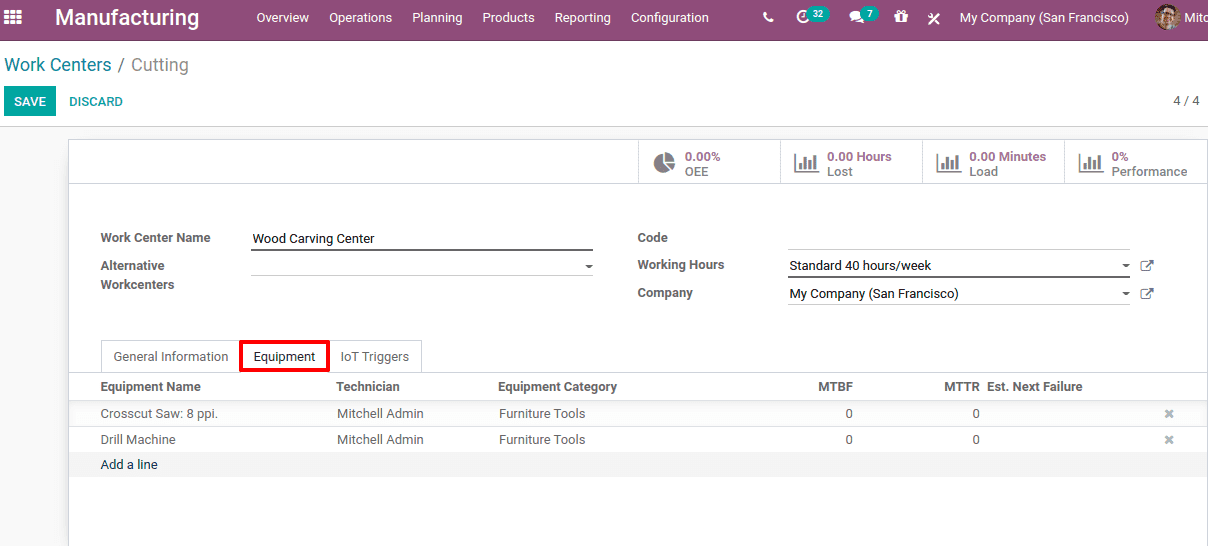
Each work center's operations are the processes that must be completed. Odoo Manufacturing Module > Configuration > Operations > Create is where operations are created.
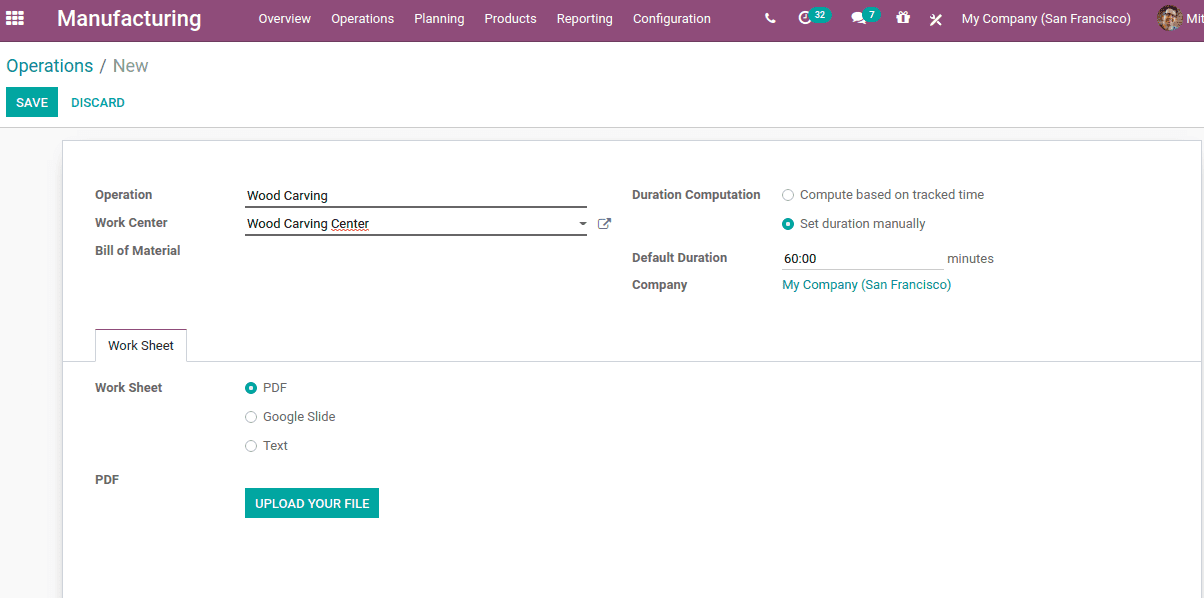
The operation or task that must be completed in the work center in order to produce the product.
Work center: The work center where the operation is located.
Computation with a time limit: There are two forms of computation with a time limit:
1. Calculate according to tracked time: the track time can be set based on prior work orders.
2. Manually set duration: Duration can be manually set in minutes.
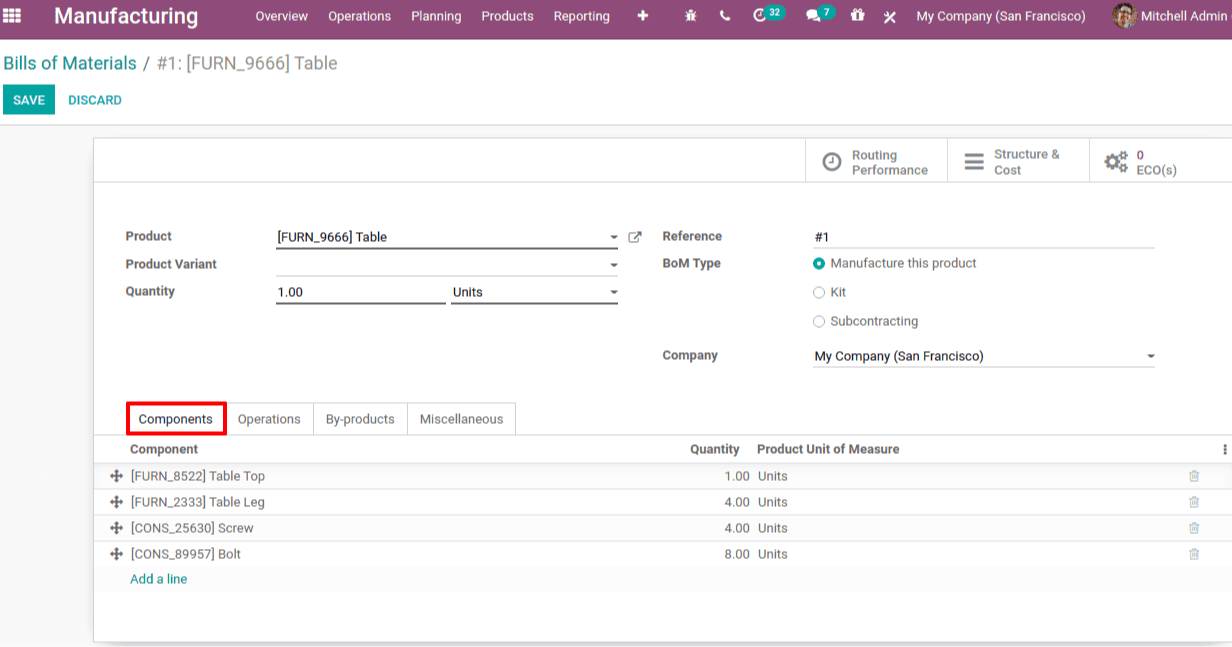
Go to Manufacturing module > Products > Bill of Materials > Build to create a bill of material for the product.
Product: The item that will be manufactured.
Product Variant: If a product variant is mentioned, only that variant is covered by the Bill of Material.
Quantity: The number of goods to be produced.
The following is a list of references for the Bill of Material.
Multiple Bill of Materials can exist for the same product.
The reference is used to identify the Bill of Materials.
The following are the types of Bill of Material:
Produce this Product in the Following Ways: The bill of materials is used to create the product.
In this situation, a product kit containing all of the BoM components is developed. As a result, they are allowed to sell the product as a kit.
Subcontracting: In some circumstances, product components are available but the manufacturers aren't experts in creating them, so they're passed off to a subcontractor.
Company: Choose from a selection of multiple companies.
Select Components from the Components drop-down menu.
Component: A component is a raw ingredient that is used to make a product.
Quantity: The number of raw materials needed to make a certain amount of product.
Product unit of measure: The unit of measure for the quantity of the product.
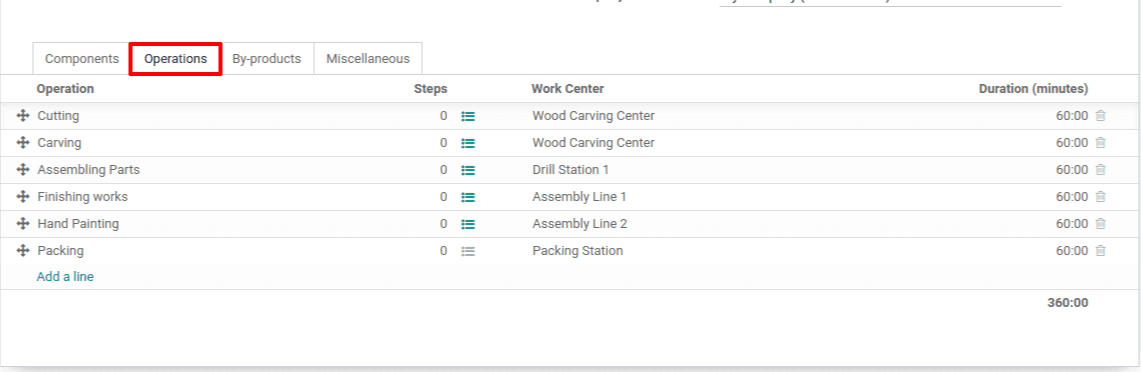

Under ‘produced in operation, the operation in which the "by-product" is created is stated. Manufacturing readiness and flexibility options can be added to the Miscellaneous tab.
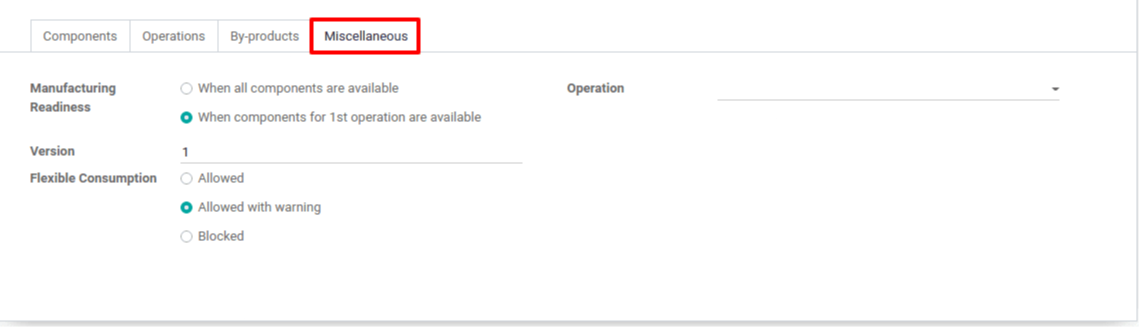
Manufacturing Readiness: Determines when the manufacturing process will begin.
When all of the components are in place- The manufacturing process may begin after all of the items are in place.
When the first operation's components are available- The manufacturing process begins when the first operation's components are available.
Version: This is the version of the product that will be manufactured.
Consumption flexibility: Defines whether or not fewer or more components can be utilized than those stated in the BoM.
Allowed: All manufacturing users have the ability to alter the amount on the bill of materials.
Allow with Warning: When the MO closes, all manufacturing users are able to alter the Bill of Material quantity with a summary of the difference in consumption.
A manufacturing order can only be closed by a manager.
After you've completed all of the configurations, go to Odoo Manufacturing Module > Operations > Manufacturing Orders > Generate to create a manufacturing order.
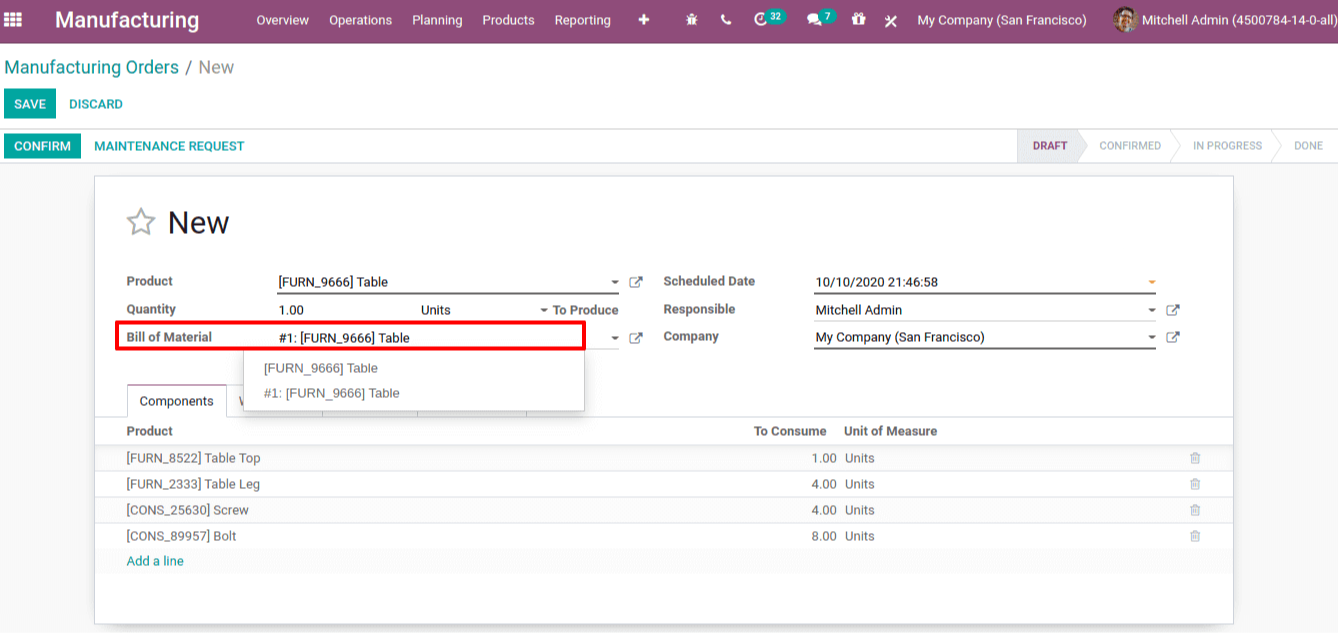
It will take you to a form where you can enter the goods and quantity you want to create.
From the drop-down menu, select the Bill of Material. The reference is used to identify each Bill of Material.
Add the planned date:
The scheduled date is when you want to begin the project.
Include the name of the person in charge as well as the name of the firm.
Save and confirm your order now.
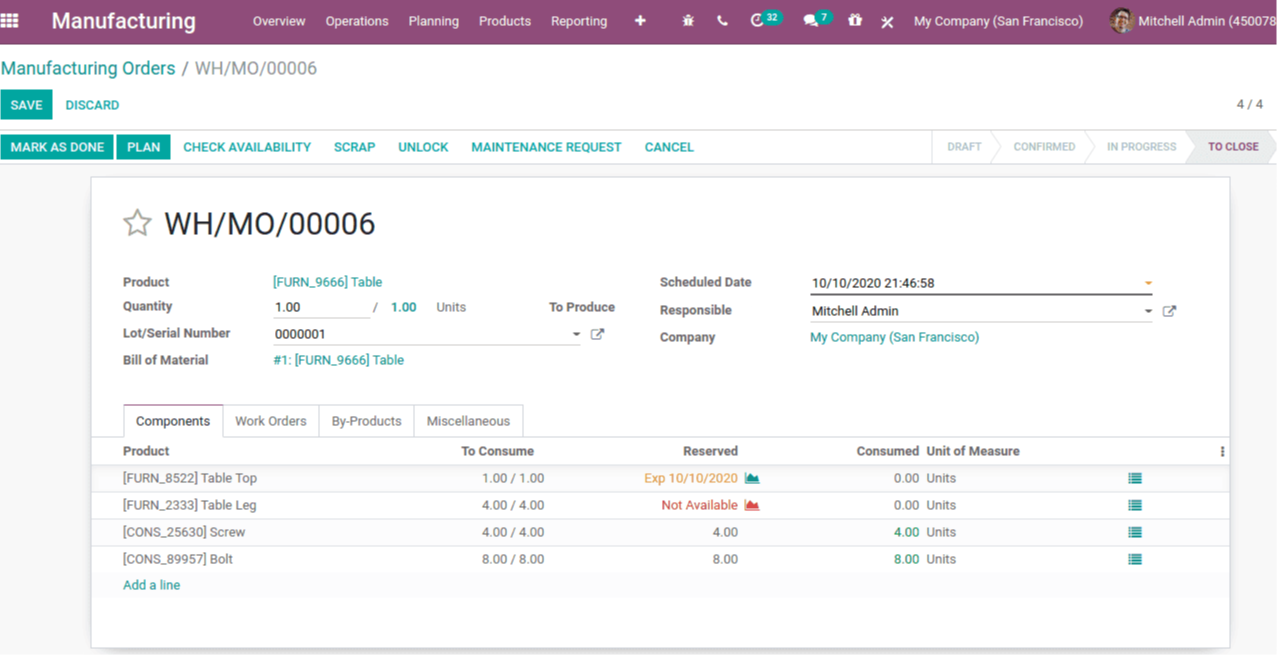
The product's Serial Number can be assigned from here. The availability of components may also be viewed here. The quantity available is indicated in green next to the quantity used. Because the ‘Table leg' is not available and the tabletop has arrived on time, the production order can be planned once all of the goods are ready.
Odoo Manufacturing Order