Managing Production in Odoo 17
To initiate production in Odoo 17, you can start by accessing any work order from the manufacturing order or by navigating to Operations -> Work Orders. This interface provides a comprehensive overview of all active work orders, enabling efficient management and execution of manufacturing tasks.
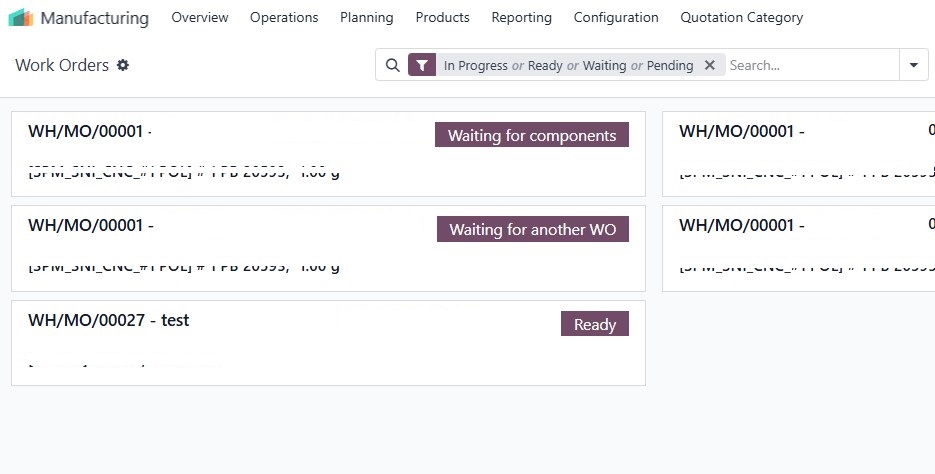
Each work order in Odoo 17 allows you to oversee and complete production tasks. Products move through predefined production routes that streamline their assembly or manufacturing process. Upon completing production tasks, the finished products are automatically added to your inventory, ensuring seamless updates and accurate stock management.
Bill of Materials (BOM) in Odoo 17
The Bill of Materials (BOM) in Odoo 17 consists of the components required for manufacturing specific products.
Each product has its own unique set of raw materials that are essential for its production.
To begin manufacturing a product, it is crucial to access and utilize the corresponding Bill of Materials.
Creating a Bill of Materials
By creating and managing BOMs in Odoo 17, manufacturers ensure accurate planning and execution of production tasks, optimizing resource utilization and maintaining consistency in product quality.
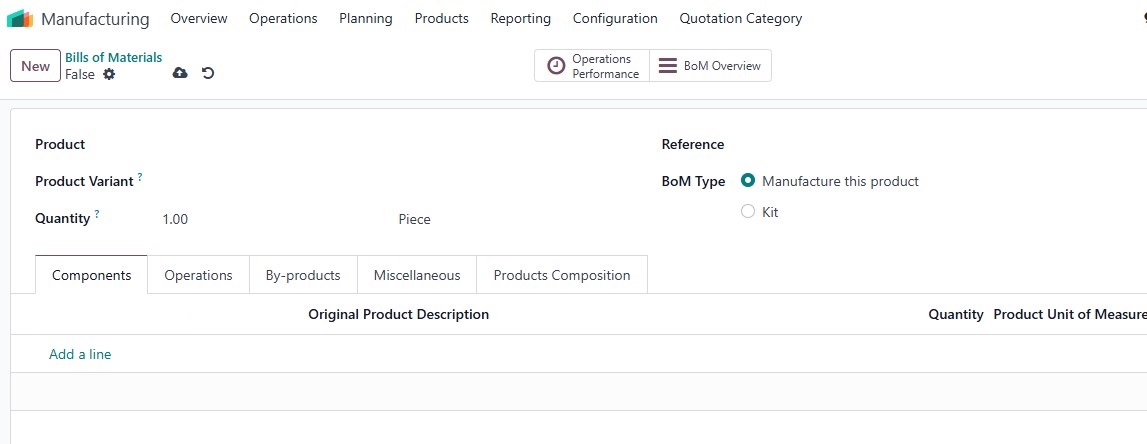
- Start by selecting the product for which you want to create the BOM.
- If the product has variants, choose the specific variant(s) applicable to your manufacturing needs.
- Enter the quantity of the product you intend to manufacture using this BOM.
- Select the production route that outlines the manufacturing process for this product.
- Optionally, assign a reference number or identifier to the BOM for organizational purposes.
- Choose the BOM type based on your manufacturing requirements:
- Manufacturing this product
- Kit (for assembly of multiple products into a single kit)
- Subcontracting (for outsourcing parts of the production process)
- Specify each component and its quantity.
-
If there is any by-products generated during the manufacturing process, add them to the BOM as well
- Once all necessary fields are filled out, click on the "Save" button to create the Bill of Materials.
Managing Scrap in Odoo 17 Manufacturing
Scrap management is a valuable feature in Odoo 17 Manufacturing, allowing users to handle discarded materials at any stage of the production process. By utilizing these features, manufacturers can efficiently manage waste materials, ensuring streamlined operations and accurate inventory management in Odoo 17 Manufacturing.
Alternatively, users can manually create scrap orders by navigating to Manufacturing -> Operations -> Scrap Orders -> Create. This method provides flexibility in documenting and managing scrap items as needed.
Unbuild is a versatile feature in Odoo 13 Manufacturing that allows users to disassemble a manufactured product, particularly useful when parts are damaged without necessitating the scrapping of the entire product.
Subcontracting is a process where a company sends raw materials to a subcontractor, who then uses these materials to manufacture products on their behalf. Once the manufacturing is complete, the subcontractor returns the finished products to the company.
Advantages of Subcontracting
Subcontracting offers several advantages for companies:
- Cost Efficiency: It can lower production costs by utilizing external manufacturing capabilities without investing in additional infrastructure.
- Specialized Expertise: Subcontractors often have specialized skills or equipment that may not be available in-house.
- Flexibility: Allows companies to manage fluctuating production demands more effectively.
- Focus on Core Activities: Enables companies to concentrate on core business activities while outsourcing non-core manufacturing tasks.
In Odoo 17 Manufacturing, the subcontracting feature supports these advantages, providing a structured approach to managing subcontracted production processes efficiently.
When planning to subcontract manufacturing tasks in Odoo, you can create a specific Bill of Materials (BOM) tailored for the subcontractor.
Reporting in Odoo 17 Manufacturing
Odoo 17 Manufacturing offers robust reporting features that provide insights into various aspects of production and equipment effectiveness.
Types of Reports Available:
- Manufacturing Order Reports: These reports detail the status and progress of manufacturing orders. They provide visibility into production timelines, resource utilization, and order fulfillment.
- Work Order Reports: Work order reports focus on individual tasks within manufacturing processes. They track the execution of specific production activities, including labor hours, materials used, and completion status.
- Overall Equipment Effectiveness (OEE) Reports: OEE reports measure the efficiency of equipment and machinery in the manufacturing process. They analyze factors such as availability, performance, and quality to assess overall equipment productivity.
Customization and Filtering:
- Filtering and Grouping: Users can filter and group data within each report based on specific criteria such as date range, product type, or production line.
- Customization: Reports in Odoo 17 Manufacturing are customizable, allowing users to adjust layouts, add or remove fields, and tailor the presentation of data to meet specific reporting needs.
- Save Favorite Reports: Users can save frequently used or preferred report configurations as favorites. This feature simplifies access to essential data and streamlines reporting workflows.
Odoo 17 Manufacturing's reporting capabilities empower businesses to monitor production performance, optimize resource allocation, and make informed decisions to enhance operational efficiency.
Manufacturing Module Odoo 17 - 2