Odoo 14 Manufacturing Module-Unbuild Orders Management
To construct is to build. So, what exactly is unbuild?, Unbuild is the inverse of building.
That is, unbuilding a thing implies separating its components. In the manufacturing industry, we may be required to deconstruct two different sorts of products. The first is a product produced by our own company. The company's acquired product is the second type.
Can we complete the deconstruction process without any documentation?
No. Unbuilding, like any other task in an enterprise, must be documented and managed through an appropriate channel. We must also employ a software program to coordinate this process. To guarantee industry openness, unbuilding and other facts must be recorded into the document.
What is Odoo Manufacturing?
Odoo Manufacturing is a tool that offers all of the features and operations needed to run a manufacturing business efficiently. Odoo Manufacturing provides product manufacturing support by producing manufacturing orders and other paperwork.
Manufacturing order management
- Work order management
- Scrap order management
- Unbuild order management
- Product management is the feature of Odoo manufacturing.
- Material management bill
- Control of lot/serial numbers
- Management of product variants - Master Production Schedule - Report analysis
Unbuild Orders in Odoo
Odoo Unbuild orders can assist you in two ways.
1. To disassemble a product made by your own company
2. To deconstruct a product developed by another company and purchased by yours,
When will we want to deconstruct a product?
It could be for a variety of causes. The first possibility is that the merchandise has been damaged.
Even if the product is unsellable, you may not have to scrap it entirely because only one or two components utilized in manufacture may be broken. We can then separate these components and store them in our raw material stock.
As an example, consider a wooden table. You might have finished making the wooden tables.
However, during the quality check, your crew notices some difficulties with the table legs. Then you don't have to throw out the entire product. Instead, you can disassemble the product and repurpose the tabletop. Only the table legs must be discarded. This saves both money and resources.
In other circumstances, a manufacturer may purchase a product from another seller in order to reuse or recycle some of its components.
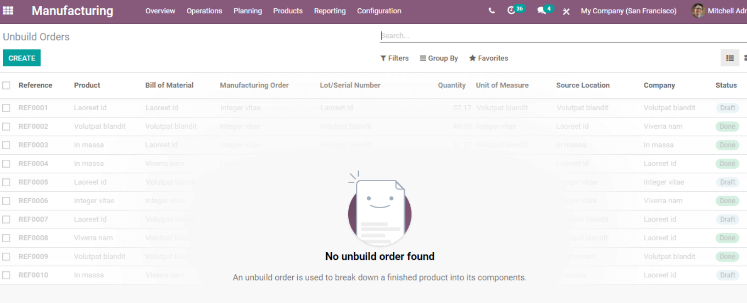
Odoo Unbuild Orders
Menus such as Overview, Planning, Operations, Reporting, Products, and Configuration are included in the Manufacturing module. We can use the Unbuild Orders option from the Operations menu here. So far, no Unbuild Orders have been prepared. As a result, we have the Create button to complete the procedure.
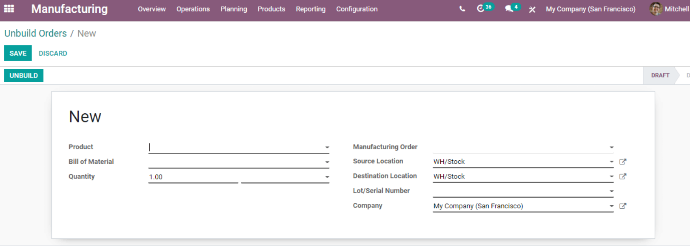
We have the unbuild form here.
The manufactured product's build order has been canceled.
First, we'll look at how to prepare an unbuild order for a manufactured product or a product made at your own company.
A few fields can be found here.
Product: Enter the name of the product you wish to unbuild.
Material List: Fill out the BoM for the product that needs to be disassembled. This will make it easier to keep track of the components and their quantities.
Quantity: The number of units to be demolished.
Manufacturing Order: If you are disassembling a product that was created at your own facility, you can include the manufacturing order details here.
Source Location: The location of the product that you want to unbuild.
The storage area to which you want to relocate the split components is referred to as the destination location.
Lot/Serial Number: This will assist the system in determining which product has been damaged or which you wish to deconstruct.
Company: The company's name
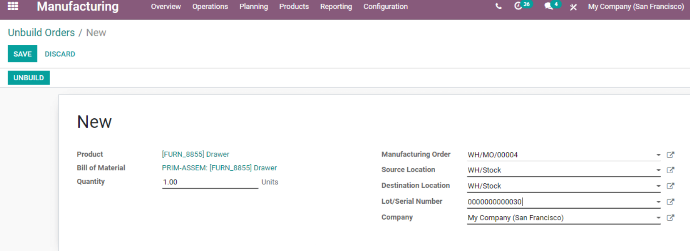
Here, I selected a Drawer, and the BoM was automatically updated. I made the decision to unbuild only one quantity. The manufacturing order can be selected using the drop-down menu.
The source location is then automatically updated. We have the ability to specify the target location. I've also included the lot/serial number and the name of the company.
Now Click on Save, then go to Unbuild. Located on the top Left.
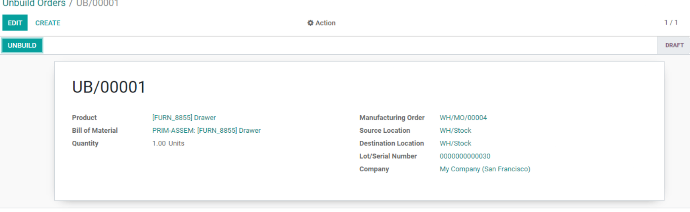
After that, the status will be changed to Done. Product Moves can also be found on the same page. This will assist us in tracing the product's movement.
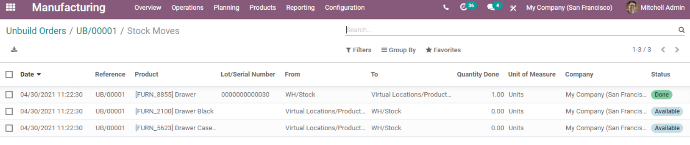
The product Drawer has been moved from WH/Stock to virtual locations/Production, as seen above. We can also observe that the components have been returned to Stock from Production. We may also retrieve the shelf number if we had mentioned it in the Bill of Material.
Unbuild order for a previously purchased product
It is now time to prepare unbuild orders for the just purchased products. This can also be accomplished with the same form.
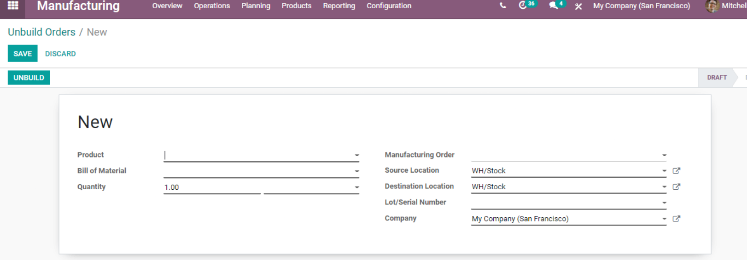
As previously mentioned, we must complete in the fields Product, Bill of Material, Quantity, Source Location, Destination Location, Lot/Serial number, and Company Details.
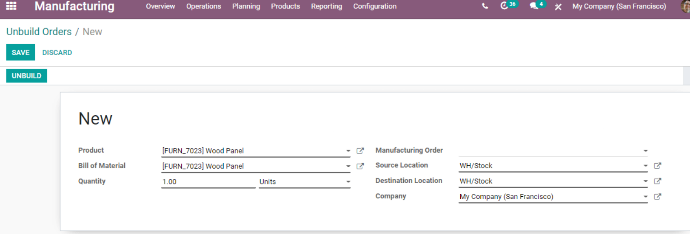
The Wood panel was picked as the purchased product. As before, the Bill of Material was immediately updated, and we may now set the quantity.
Then, because the product was purchased rather than manufactured, we do not need to submit the manufacturing order specifics here. We can include the source and destination locations, as well as company information, here. Then click SAVE and UNBUILD.
We can now monitor the product movement.
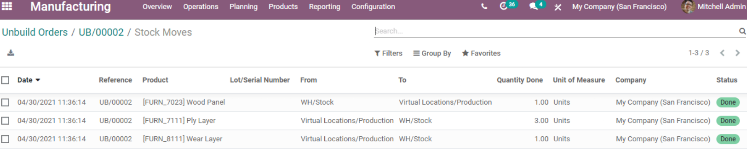
We can see here that the goods have been transported from stock to the production location. The components were then returned to the production facility. It has been moved to the warehouse.
We have already gone over the many features and functionalities of Odoo 14 Manufacturing in depth.
You can read both general and functional blogs on Odoo 14 Manufacturing Module.
We've talked about scrap order management, manufacture order management, work center management, bill of material management, lot and serial number management, and all of the other elements of the manufacturing module.
Odoo 14 Manufacturing Module-Unbuild Orders Management