Odoo Inventory Module Product Management
The features of product management in an industry are critical for efficient functioning. No matter how efficient you are in the functional parts of the organization, such as manufacturing, sales, staff management, and thorough financial control, none of this is possible without excellent product management and control of product inflow and outflow. Furthermore, being the key operational region on which all other functional instruments are built in operations, a company's warehouse operations play a critical role in the proper management of items. To oversee the entire operation, the company now uses specific management systems. Furthermore, the transition from traditional ways to current methodologies has facilitated operational control and total control in operations.
The Odoo platform is a company management tool that falls under the operational category of Enterprise and Resource Planning systems, which provide comprehensive and adequate business control capabilities. The ERP category encompasses a wide range of solutions. Among these, the Odoo platform stands out for its superior operational management, allowing for comprehensive control of business activities through the platform's specialised modules of operation.
One of the main characteristics of the Odoo platform is the modular infrastructure, which comes with complete and trustworthy business operations. There is a specific inventory management module where the different warehouses of operations may be properly controlled in terms of company warehouse management.
Additionally, the inventory module offers multiple warehouse management, which is beneficial to organizations and their numerous divisions of operations. You'll be able to successfully manage online and offline sales thanks to the consolidated inventory infrastructure. The store's retail and wholesale sales operations can be managed efficiently at the same time. The Odoo platform is also far more comprehensive than many of the inventory management products on the market today, with the ability to perform advanced warehouse operations like cross-docking and drop shipping.
Perish-ability is one criteria that should be addressed when dealing with products in grocery shops and other businesses that deal with consumables. Stock management should be based on the products' expiration dates as well as their quality. Furthermore, the company must be cautious when handling perishable products, which will be difficult to do without dedicated tools and management alternatives.
The Odoo platform offers perishable product management, which can be done successfully using the platform by establishing expiration dates and categorizing products as consumable.
The components of product management and removal based on the sales that are being conducted may be done successfully using numerous product removal methods such as FIFO- First In First Out, LIFO- Last In Last Out, and FILO- First In Last Out that can be defined using the Odoo platform. When it comes to perishable product management, the FIFO rule can be applied because the first-in products would be damaged first, thus they should all be removed before the projected expiration date.
Furthermore, products that have first expired should be removed, ensuring that no product is consumed or destroyed. Furthermore, following this process will ensure that no expired products are offered to customers, preserving the quality of the product sold as well as the organization's decorum.
To use the Odoo platform to manage the operations of perishable products, you must first configure some of the settings choices in the Inventory Module's Settings menu. Lots and Serial Numbers, as well as the Expiration Dates option, should be enabled under the Traceability option; this will ensure that all purchase processes may be completed by assigning lots and serial numbers and setting the product's expiration date using Lots and Serial Numbers. Additionally, the options under the Warehouse menu, such as Storage Sites and Multi-Step Routes, should be enabled to aid in the operational management of numerous storage locations and dedicated product movement routes that can be set.
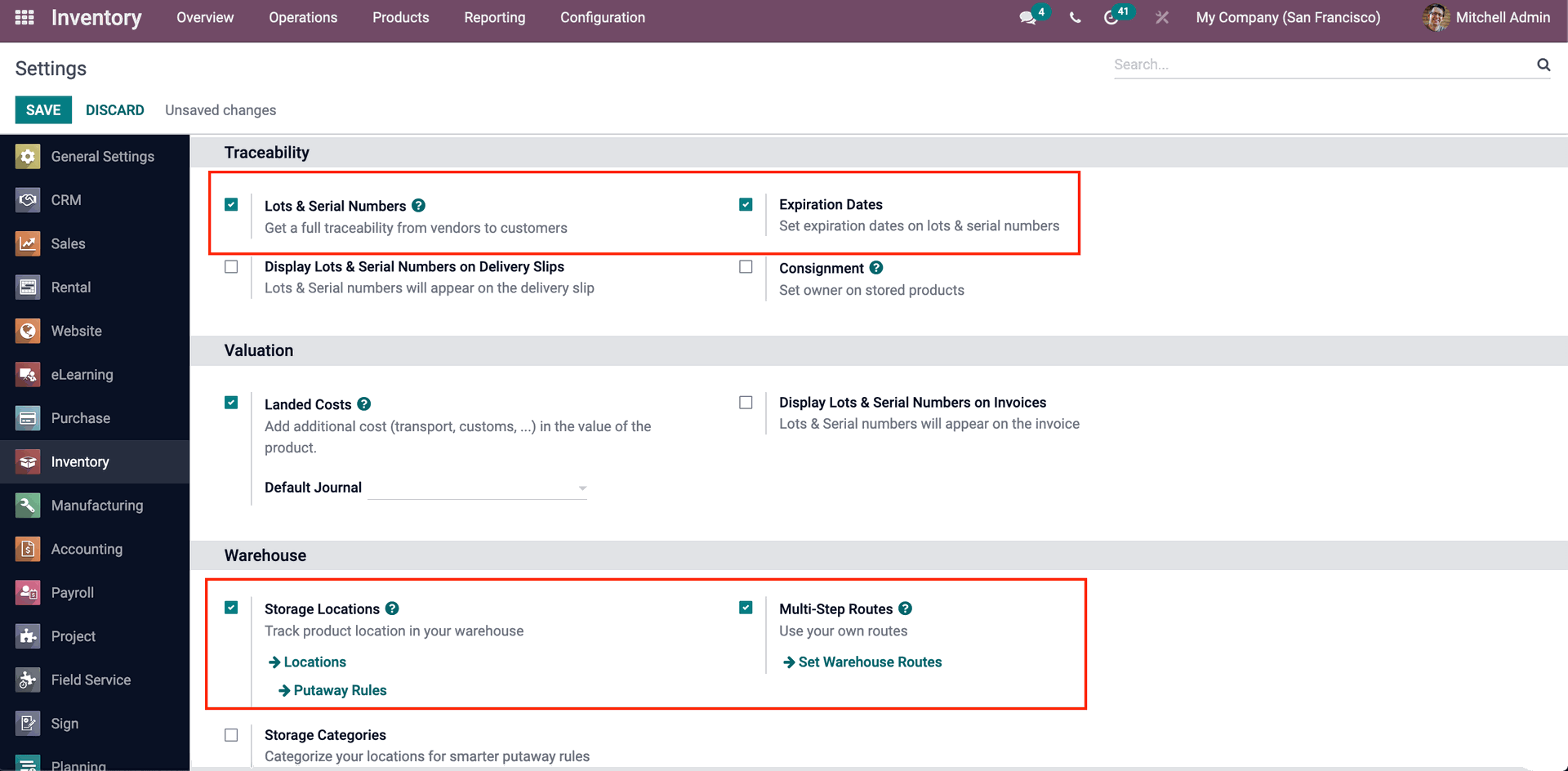
Let's move on to building a new perishable product to understand its operations in Odoo now that the Configuration options for working with perishable products have been enabled. Select the Create option from the Products menu, which will take you to the Product you created in the window, as shown in the screenshot below. Initially, the product name and type should be determined, such as whether it's a saleable, purchased, recurring, or renting product. Furthermore, all of the product's general information should be defined.
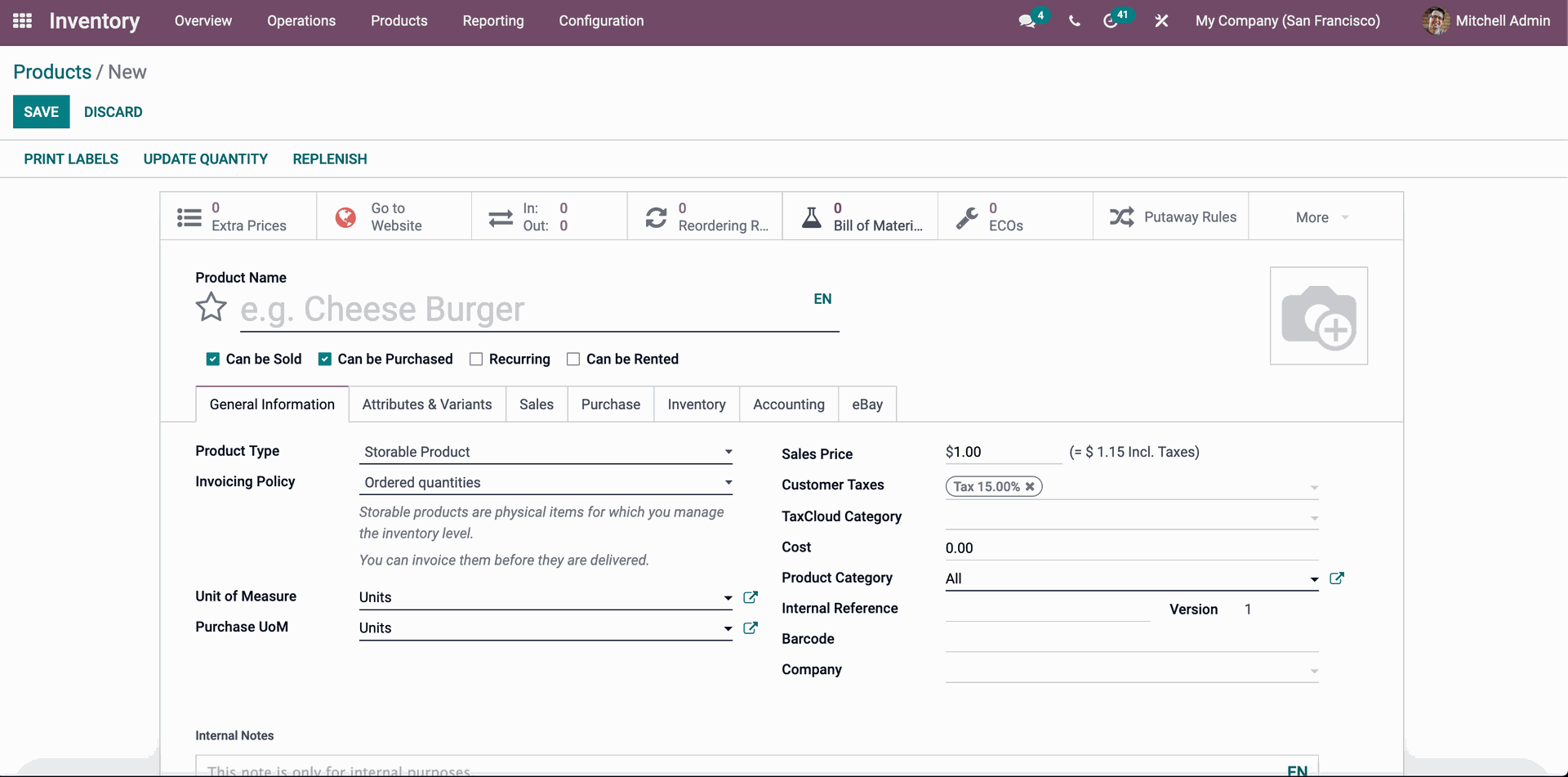
In terms of product movement and storage management, the Inventory menu will provide the appropriate configuration options. Tracing can be enabled here by using a unique serial number or by using lots. Expiration Date choices should also be encouraged, and the dates should be specified. Expiration Time, Best Before Time, Removal Time, and Alert Time for the individual product are all listed under the Dates section. The Product menu should be saved once all of these elements have been defined.
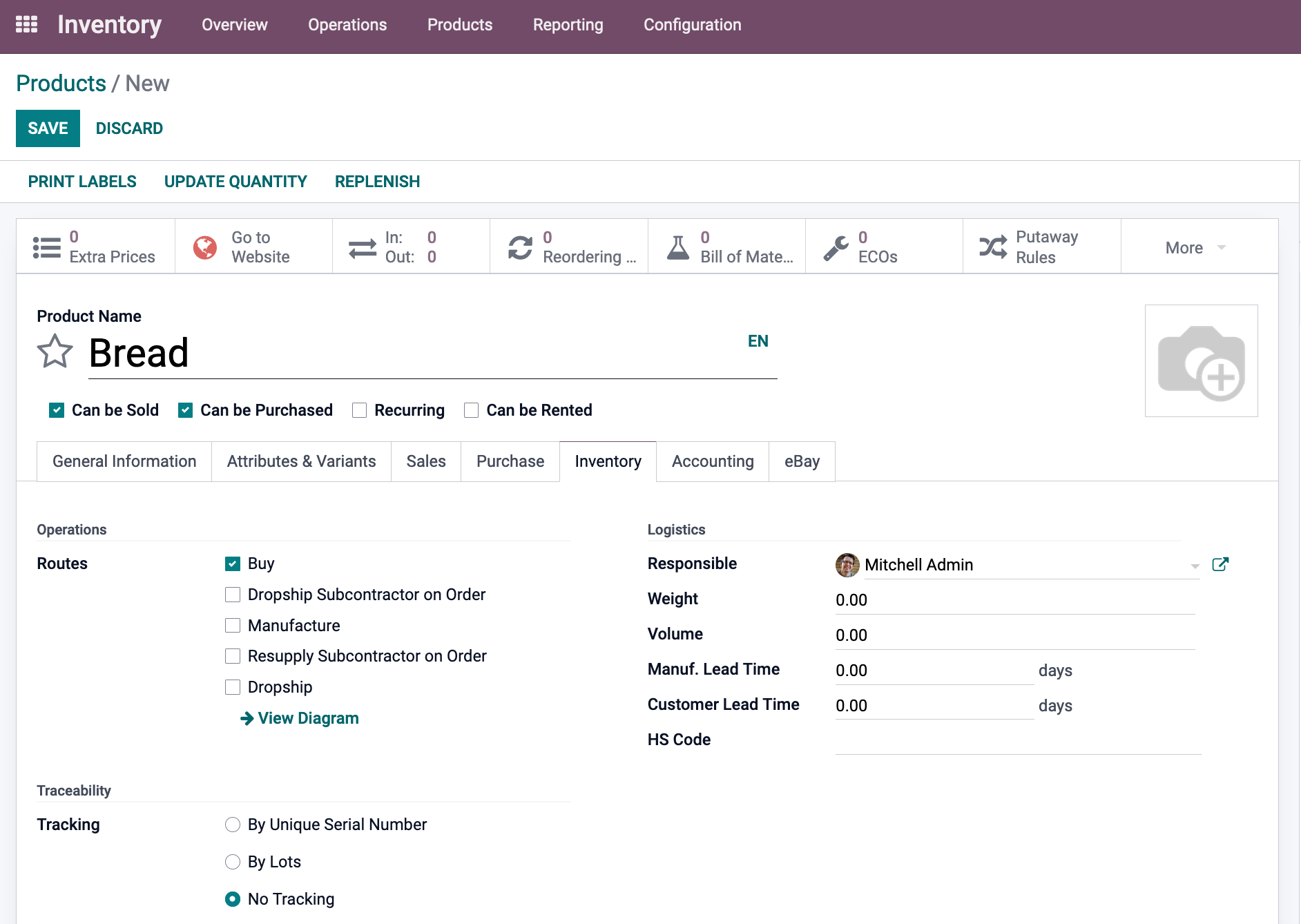
Select the storage place for the product we just generated from the Location section. The WH/Stock indicates the product's location. Furthermore, the Location pane will display all of the operations' locations. The corresponding Location can be located by using the provided Filtering and Group by options.
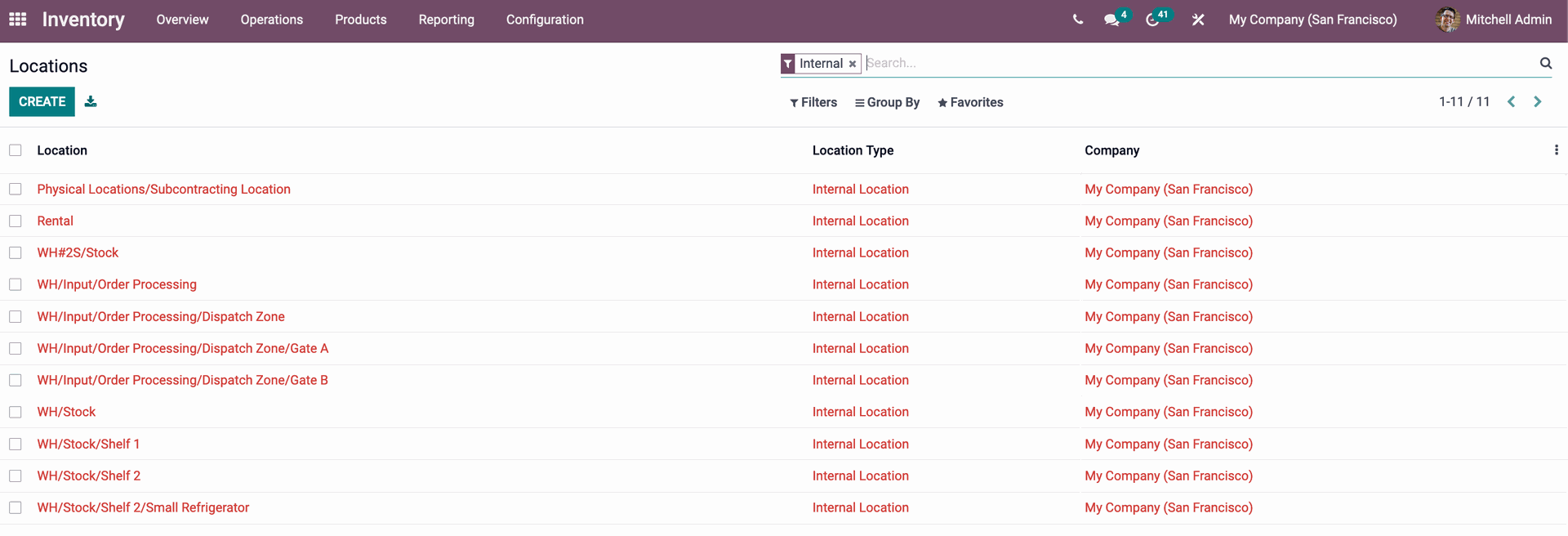
The Removal Strategy for the product can be set to First Expiry First Out (FEFO) in the respective Location configuration menu, ensuring that the product that will expire first is removed from stock before the new ones.
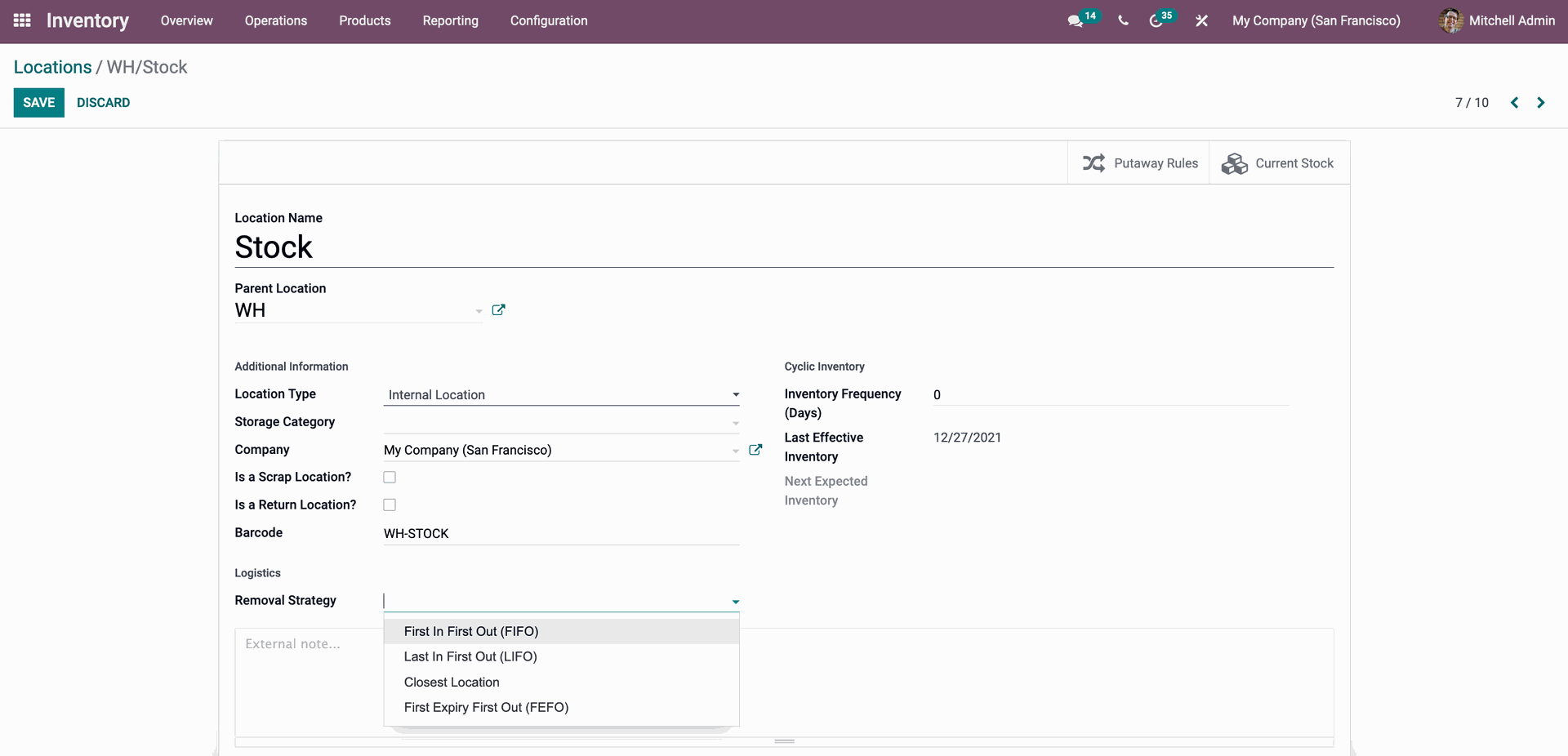
Let's make a Purchase order for the relevant items to get a better understanding of how the perishable product management system works. Let's imagine we're purchasing ten units.
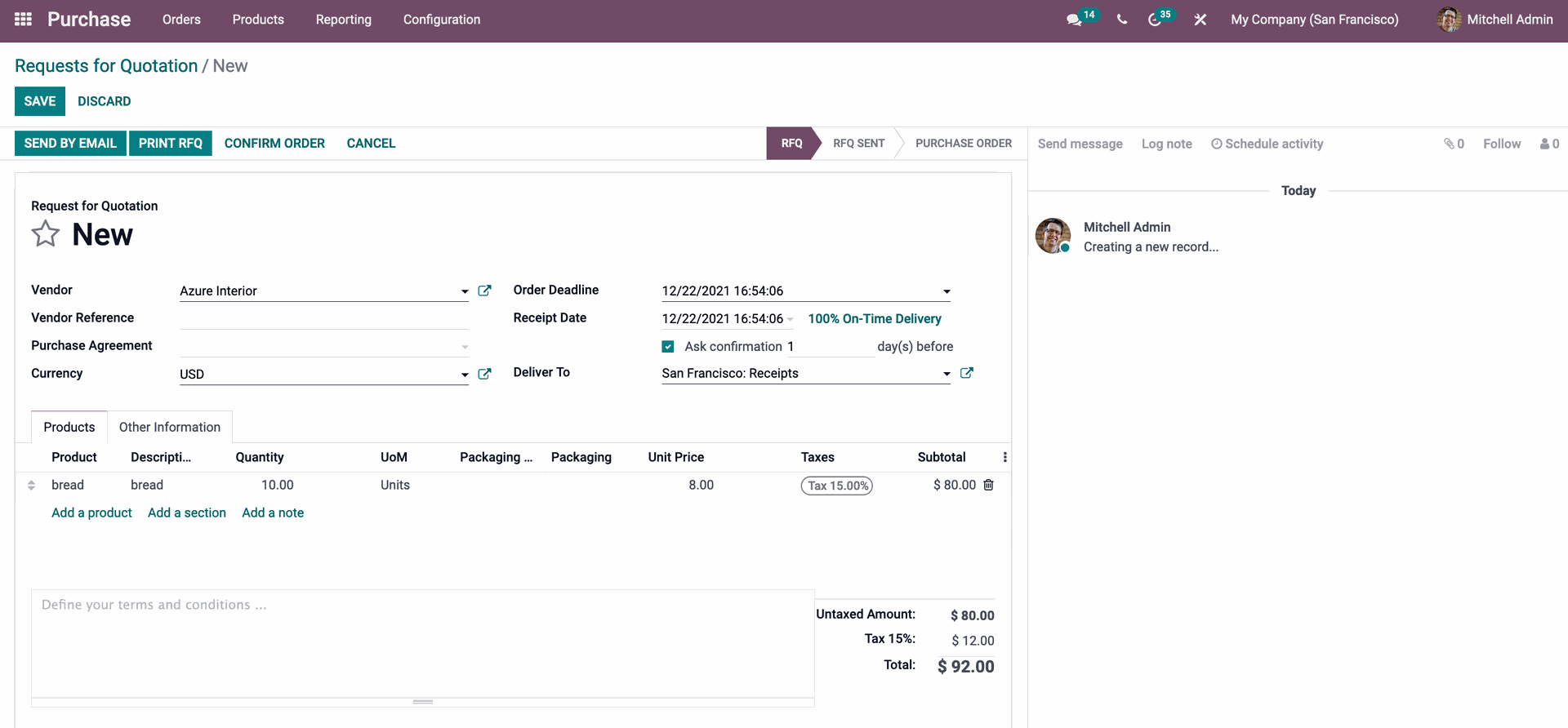
Select the Receive product option once the Purchase Quotation has been confirmed.
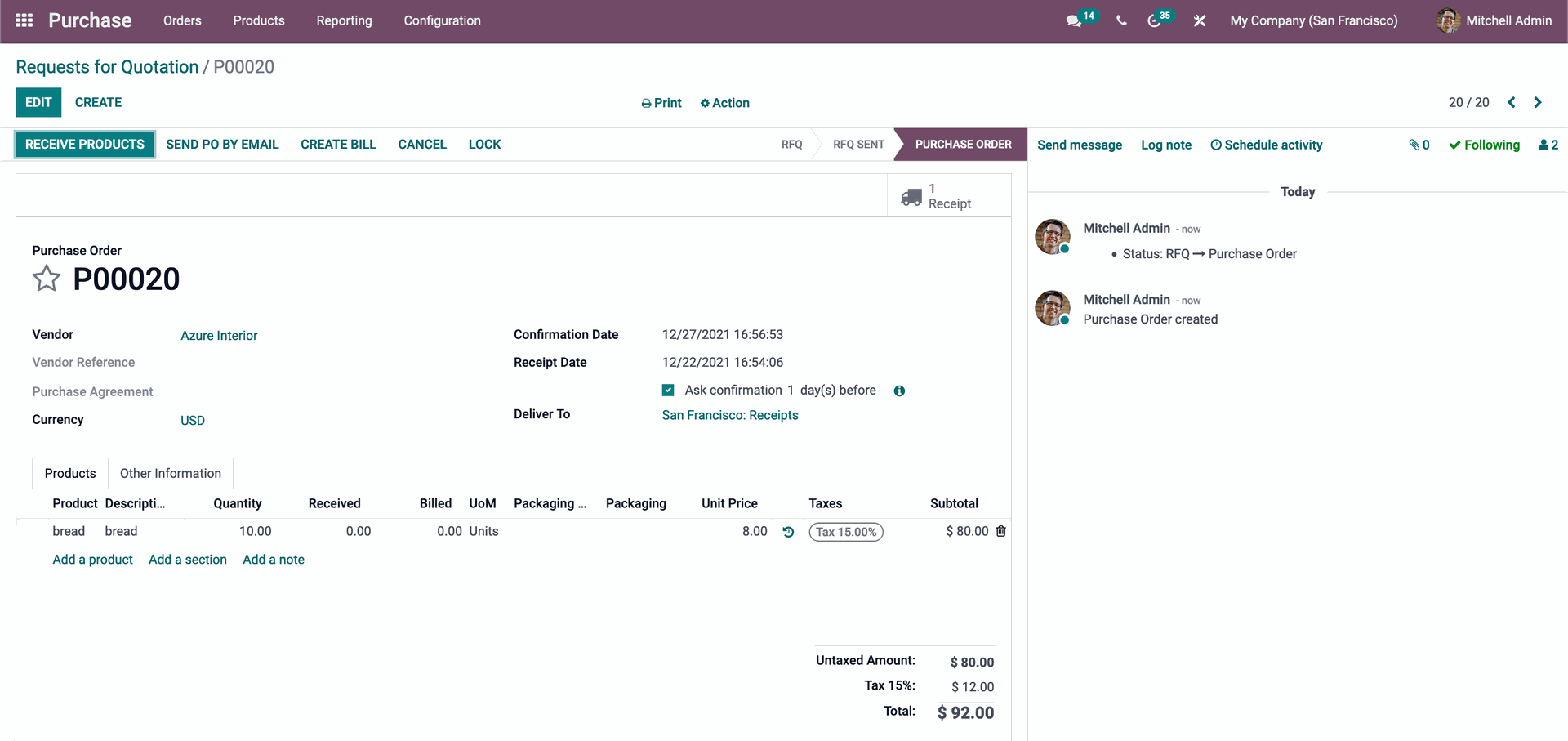
You must assign the Lot and Serial numbers for the purchase before confirming the products received. Because serial numbers are used for product tracing, the products should be assigned with the appropriate serial numbers. You can provide the First Serial Number and the Number of Serial Numbers, then choose the Assign Serial Numbers option to automatically assign Serial Numbers to all of the products being purchased. The product's Lot numbers can be assigned using the same principles.
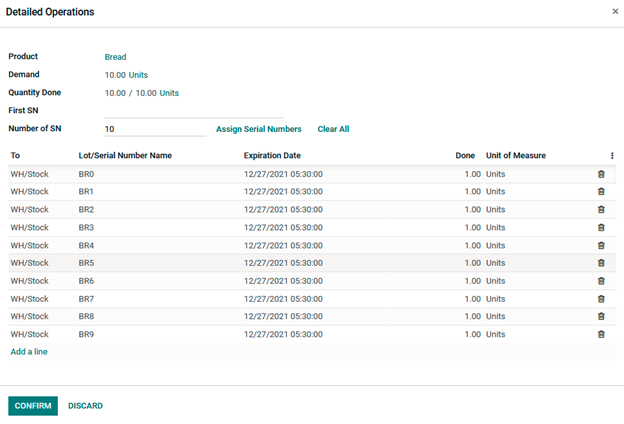
After you've defined the Lots and Serial Numbers, you'll be able to Validate the Purchase Order when the products arrive.
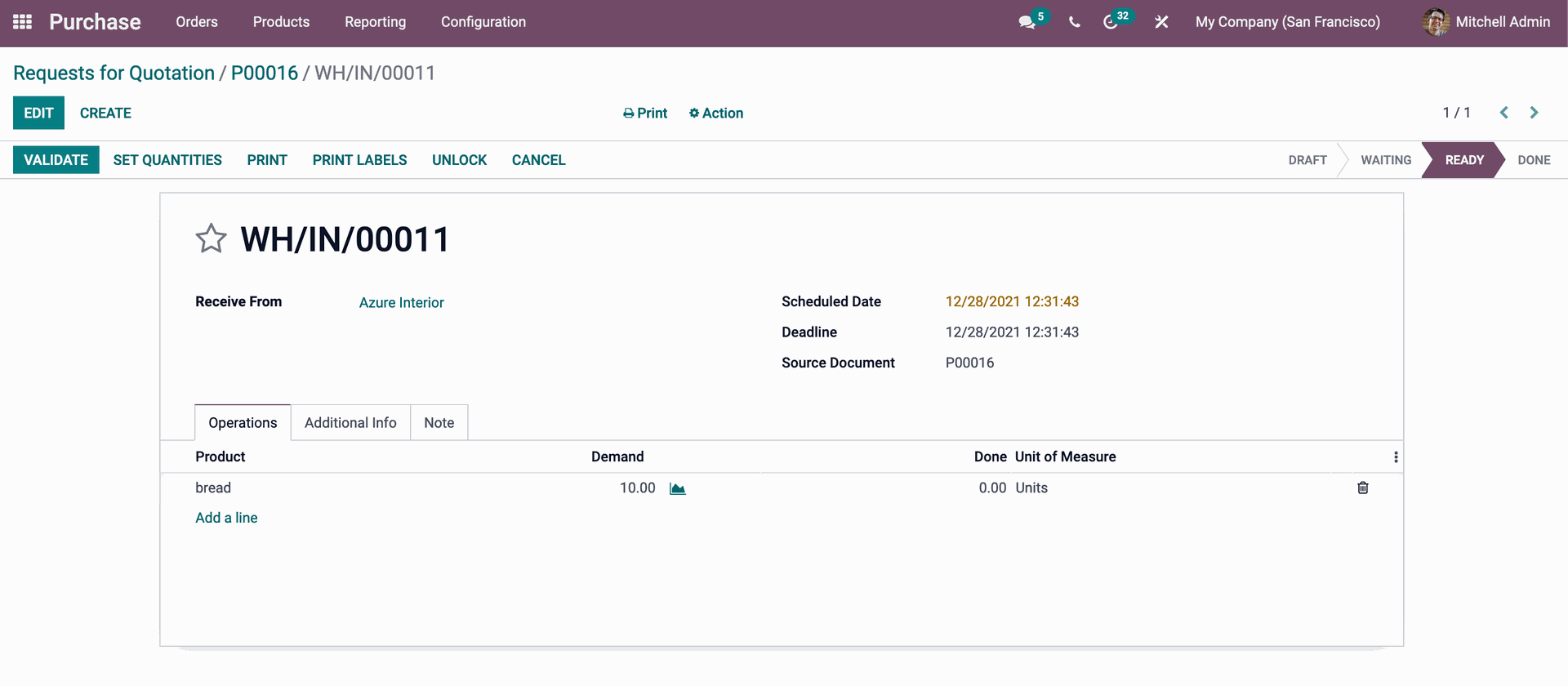
The Stock will be defined in the corresponding Product's Locations, as illustrated in the accompanying screenshot. The Serial Number and Lot Number will also be defined here, which will assist you in understanding the product's Stock information.
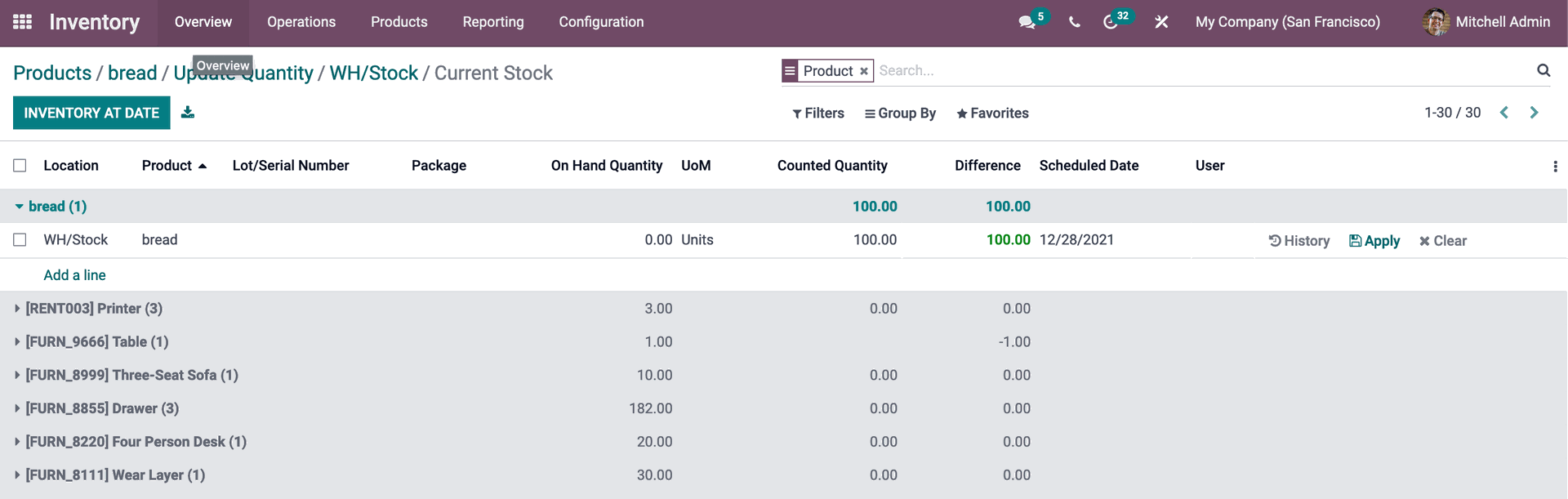
When you select a Unit from a product, the details of that Unit will be displayed to you, as shown in the screenshot below. Furthermore, the Expiration Date, Removal Date, Best Before Date, and Alert Date will be defined depending on the ones set under the product configuration after validating the Dates that have been defined.
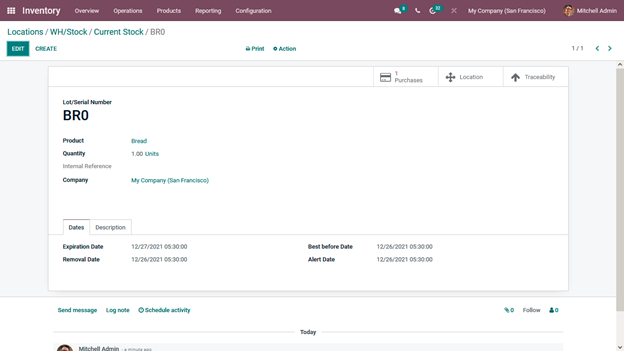
The Lot and Serial Numbers are now created when a Sales Quotation is created for a specific product with the quantity set to six numbers, as illustrated in the following screenshot.
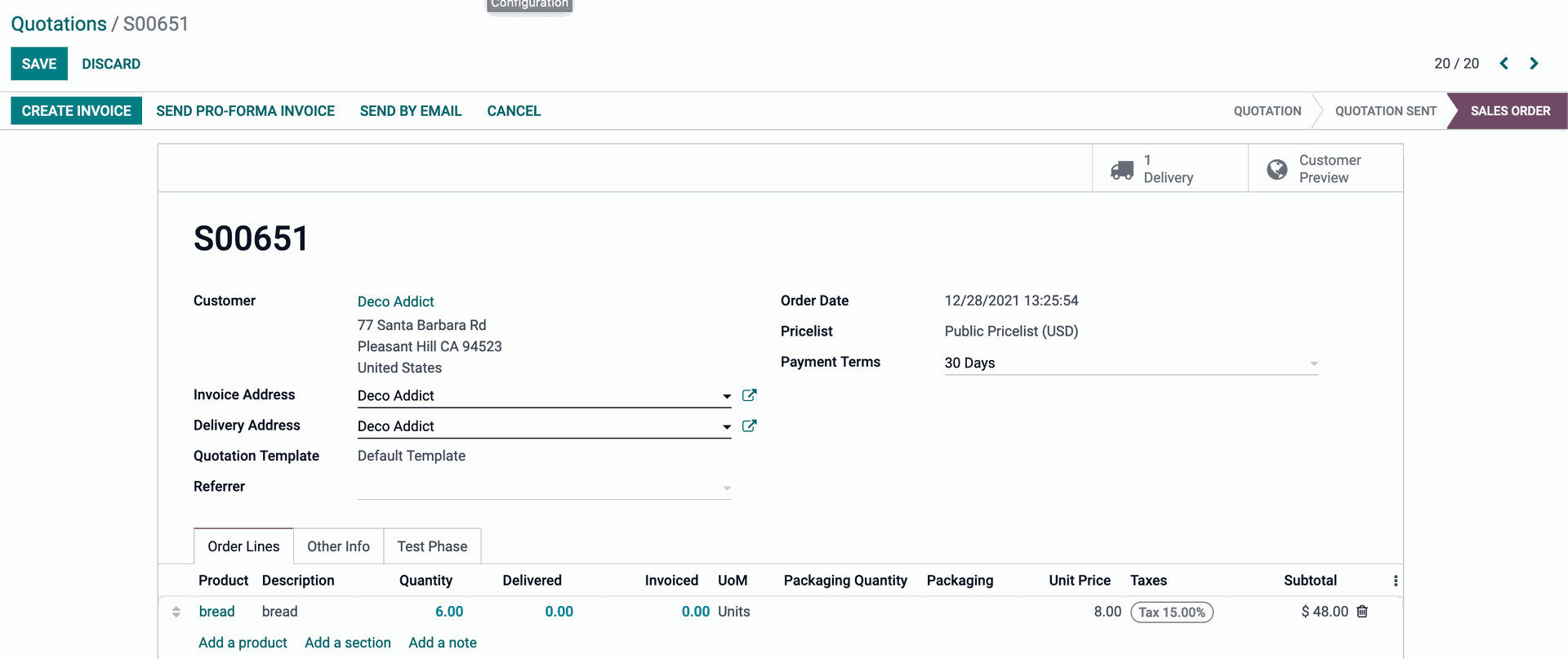
The first six goods, along with the first six Serial Numbers, will be assigned automatically. If the Lot numbers are defined, the product with the original Lots purchased will be detailed, taking the Expiration and Removal Dates into account.
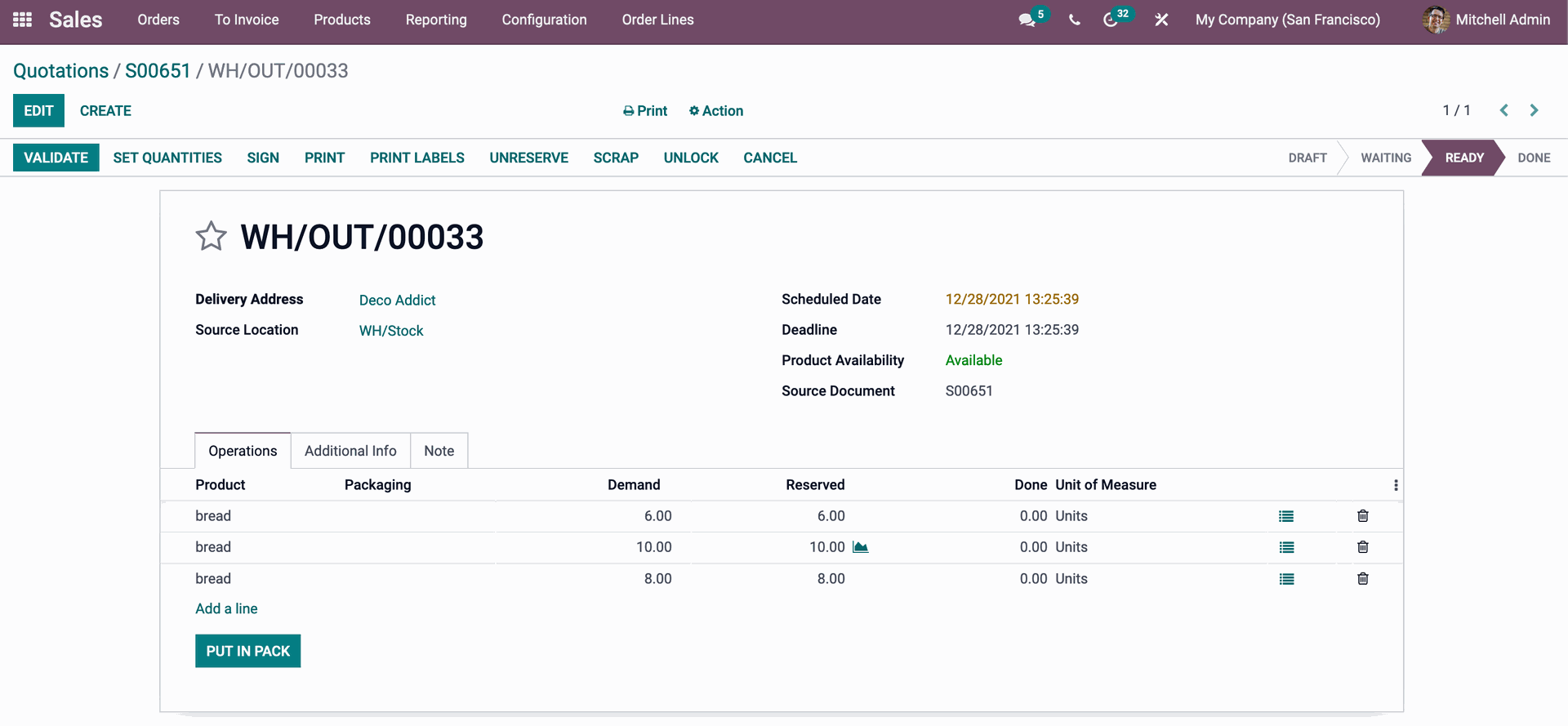
The Odoo platform's feature will ensure that the products that were brought in initially are removed from stock after the orders are received. Furthermore, the Expiration, Best before, and Removal dates will be taken into account to ensure that buyers receive high-quality products.
Odoo Inventory Module Product Management